
DEL ACCEPTS A CHALLENGE….AND PROVIDES A SOLUTION!!
In the spring of 2005 Del Packaging was chosen to develop a revolutionary overcapper that was capable of applying an overcap to a non-traditional container. Within this project Del had several challenges:
- Time– By utilizing our experience of over 20 years in the overcapping industry, Del was able meet the project’s time requirements while designing, testing, and proving a new concept capper to meet the customer’s new packaging design.
- New Container Design– the customer’s new product posed several challenges. First, the soft wall paper-board container required forming and maintaining its shape during the cap application process.
- New Overcap Design— the plunge style lid was an oval shape and could not be applied with a traditional method of stripping the overcap from a cap chute.
- Customer’s Needs— In order to meet the customer’s packaging needs, Del designed a new capping system, the model CMLP (Continuous Motion Lid Placer). The CMLP is now placing lids on the customer’s product at 220 CPM with a guaranteed efficiency rating of 99.9%.
If you have a new product application, Del will help ensure the project is a long-term success by providing high quality equipment and a guarantee of 99.9% efficiency.
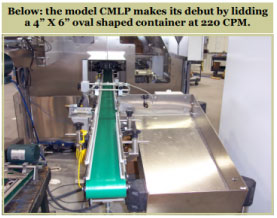
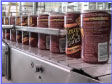
OVERCAP FEEDER
In order to feed the oval shaped cap, Del utilized our RF-6200 Rotary Feeder. The overcap had some delicate characteristics and the RF series feeder, with its ABS plastic center disk provides consistent output without damaging the overcaps.
Overcap Pick-up
The CMLP utilizes an interchangeable vacuum chuck system to pick the overcaps from the cap conveyor. The vacuum chucks travel on a cam system and ensure precision placement every time.
Container Forming
The soft walled paper-board containers required forming and maintaining their shape during the cap application process. Del utilized a precision cradle block system on horizontal cams in order to accomplish this task.
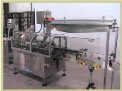
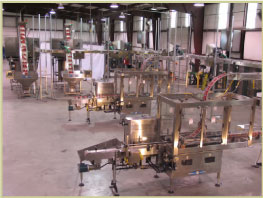
Above: Model ASRL-CC Overcapper capable of running almost any shape container up to 400 CPM.
Right: Automatic cup loader configured to interface with your existing spinning rod cap feeder.
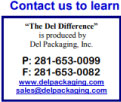