
SOLUTIONS TO NEW PACKAGE DESIGNS
As new package concepts are introduced there is often little consideration toward
automation. We see projects typically driven on the basis of differentiating from the
competition; not how the new package will impact the production line and it’s efficiency. Del’s
challenge is to offer a solution that will satisfy the needs of the plant without sacrificing the
design and functionality of the “new and improved” package.
One of Del’s strengths is its ability to think outside the box to offer solutions with an emphasis
on utilizing proven technology. This approach has worked well over the years yielding
significant returns as expressed by our satisfied customers.
SHAPES OF THINGS TO COME
The traditional round container is losing ground to new innovative shapes and sizes. These new designed lids and containers sometimes include items such as scoops and leaflets. These require complex solutions to address part feeding, conveying, and lidding.
Del is in a unique position to provide all the necessary components to offer a complete turn key solution.
TAPPING INTO DEL’S EXPERIENCE
Over the years Del has collaborated with some of the largest multi-national companies during the package design phase to improve the automation process. Del works directly with the buyer and their suppliers to incorporate features to the design that are proven to aid in the packaging process. To help refine these features Del conducts extensive systems engineering and testing to minimize risk and assure a successful product launch. Reference figure 1 below.
THE IMPORTANCE OF TESTING
Even the greatest ideas on paper still have to be proven before signing off on the project. Before the metal cutting starts a series of prototypes (caps, containers, scoops) are produced for evaluation and testing purposes. Del will fabricate test fixtures to prove the principal concept and document the results. The buyer is an active participant in the testing process and comes away with a better appreciation for the changes that are needed to make a
better performing package. These tests can include:
• Cap feeding to verify rates and efficiencies
• Lid application tests to confirm and validate lid alignment and application pressure requirements.
• Scoop feeding, orientation, placement
• Container handling and conveying
• Vision inspection to identify color, contrast, embossing or presence of an item. Lighting requirements are established to determine the best combination to use with our detection, inspection and rejection systems.
DESIGN ENGINEERING
A thorough design review is conducted by Del’s mechanical and electrical engineers early on in the project. The buyer will typically submit a bid specification or inform Del of any specific requirements needed to meet corporate and plant expectations. Essential information pertaining to the buyer’s bid specifications are reviewed and implemented at the direction of the buyer.
Line layouts are incorporated with the buyer’s production line, making the best use of the space available while at the same time creating an ergonomic environment for the line operators and maintenance personnel. Detailed layout drawings of the plan and elevation views are provided confirming panel locations, air and power drops, operator side, and line height. All systems are thoroughly documented to provide support for the buyer at any time in the future.
The final product is a result of design reviews by our mechanical and electrical staff. This makes for an exceptional quality system which will perform at its peak performance for many years to come.
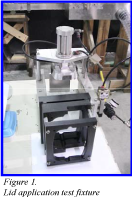

SYSTEMS ENGINEERING
Del’s experienced engineering, manufacturing, and assembly teams offer a variety of solutions to your specific packaging application.
TAMPER EVIDENT HEAT SEALING: Del offers indexing and continuous motion heat sealing system utilizing proven technology.
OVERCAPPING: Del has been manufacturing overcappers for more than 40 years. We manufacture various models utilizing belt drive and cradle block designs to handle virtually any shape and size with speeds up to 600 containers per minute.
LID PLUGGING: Del manufactures three types of lid plugging systems for a variety of overcap and lid styles.
CAP FEEDING: Spinning rod cap feeders, rotary parts feeders, and elevator sorter feeders.
CONTAINER CONVEYING: Table top, belting, side flex, and air conveyors. Lane merging and dividers are also available.
CUP AND TUB DENESTING: Single lane and dual lane container denesters for microwavable containers, cups, tubs, trays, and pails.
CUP AND TUB RESTACKING: Del manufactures restacking equipment for round and non round tapered cups and tubs.
SCOOP FEEDERS – PLACERS: Del can integrate feeders and placers for your specific application.
LEAFLET – COUPON INSERTERS: Del can feed flat and pre-folded paper stock at high rates of speeds into a container or between the cap and sealed container.
INSPECTION – DETECTION – REJECT: We have various types of detection and inspection equipment which is used with our other equipment to verify orientation, product color, presence of scoops, presence of lids, labels, SKU coding, or for any other type of verification purposes.
CAP AND CONTAINER ORIENTERS: Del designs and manufactures systems to detect and properly orient caps and containers
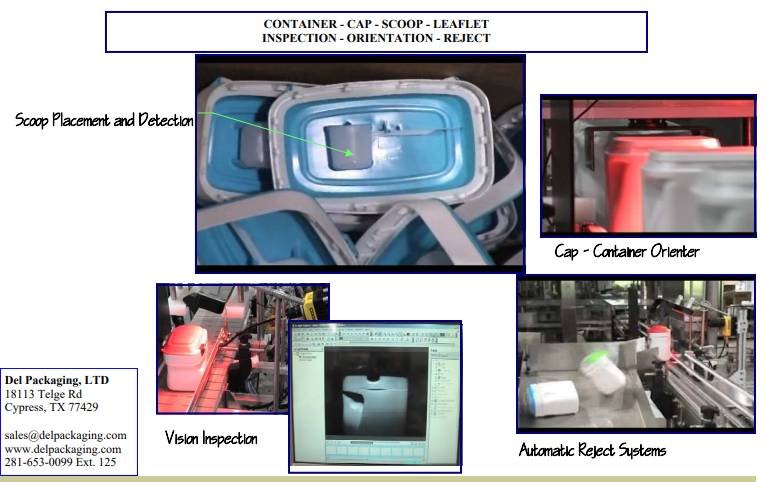